Custom Hydrogel
Manufacturing
Alliqua provides custom manufacturing solutions to partners in the medical device and cosmetics industry, utilizing our proprietary hydrogel technology.
Hydrogels are gel-like or colloidal substances made of water and solids. Hydrogels can be customized for various transdermal applications to address market opportunities in the treatment of wounds as well as the delivery of numerous drugs or other agents for pharmaceutical and cosmetic industries.
Current and Potential Hydrogel Applications
- Transdermal drug delivery
- Wound care
- Components for medical devices
- Cosmetic patches and masks
- Conductive and non-conductive adhesives
- Temperature management
- Medical diagnostics
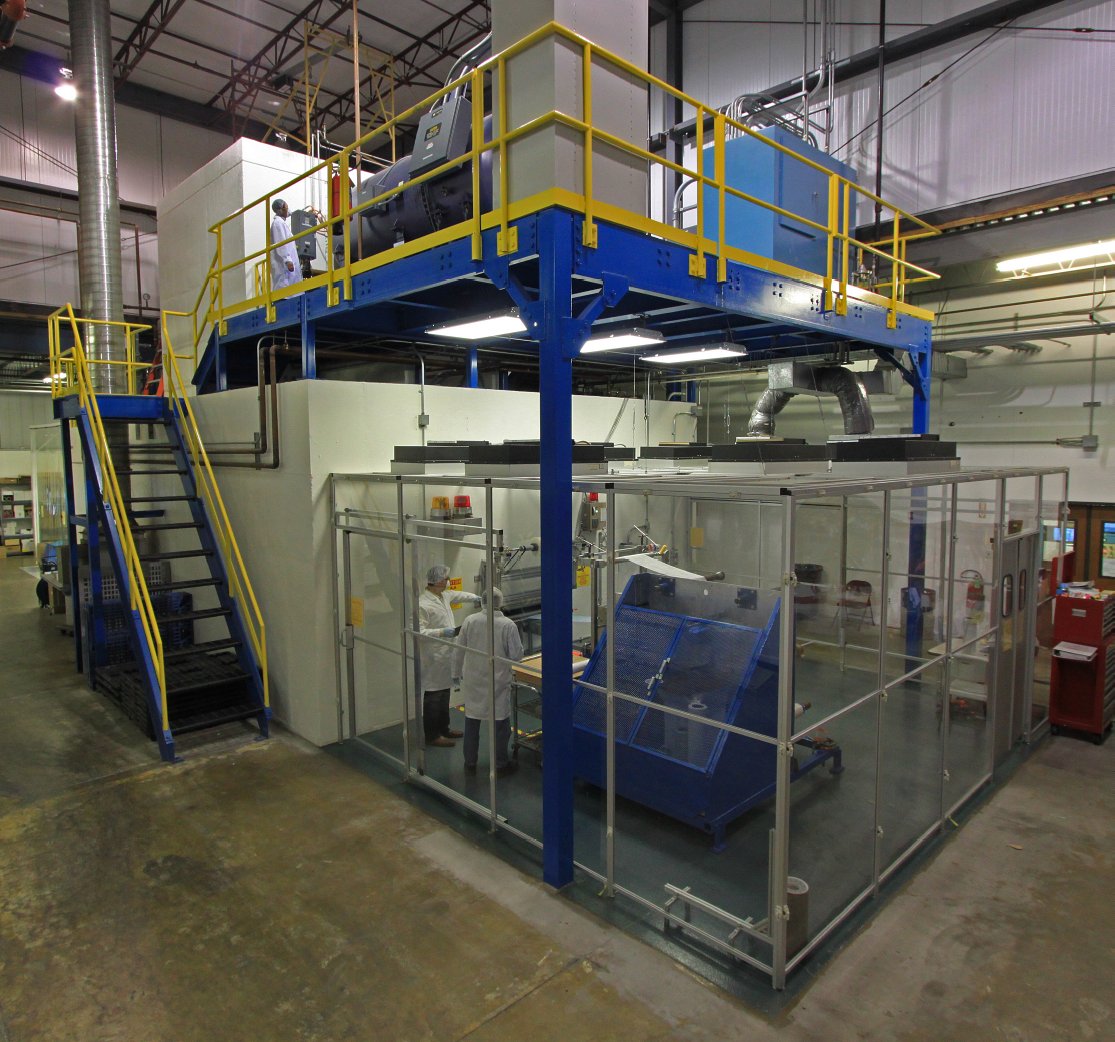
Alliqua’s 16,000 square foot GMP manufacturing facility in Langhorne, PA allows for the development and custom manufacture of a wide variety of hydrogels.
Manufacturing Process
Alliqua hydrogels are manufactured by introducing a hydrophilic polymer, which is a polymer that has a tendency to mix with or dissolve in water, into water to create a feed mix. The feed mix is then coated on to a liner and exposed to radiation. The polymers we use, when exposed to radiation, cross-link faster than they degrade, creating a matrix that gives the gels a solid form.
Active ingredients such as prescription or over-the-counter medication, skin care ingredients or wound-healing or other materials can be added before or after cross-linking. Materials that do not survive the irradiation process, or are modified by such process, are added after the cross-linking process is completed.
Once the products have been mixed and cross-linked, they form sheets that can either be delivered directly to customers or first cut and shaped according to customer or our specifications, as appropriate. We believe that many of the processes described above are proprietary to us and provide us with competitive advantages, including our production of a high quality product and our increased ability to customize products for customers.
Langhorne, PA manufacturing facility.
Advantages of Electron Beam Cross-Linked Hydrogels
Hydrogels can be created chemically, through a combination of ultra violet cross-linking and chemical interface, or by mixing a polymer and water, and then exposing it to an electron beam creating a “sheet” of water. We believe that electron beam cross-linking:
- Allows for precise control of the amount of polymer cross-linking
- Obviates the need for chemical cross-linking agents which may interfere with other additives or active ingredients
- Provides the ability to consistently manufacture high quality hydrogels
The cross-linking of hydrogels can be further modified by varying the percent of polymer cross-linking and the way in which the high energy field is delivered. There are three variables in the use of an electron beam accelerator for cross-linking of hydrogels:
- Time of exposure of the target material to the electron stream
- Voltage (electrical potential)
- Amperage (strength of the electrical current)
What Makes Alliqua Hydrogels Unique
Many of the products of Alliqua’s competition feature physical characteristics which Alliqua believes are less desirable than its own hydrogels. These include aggressive skin bonding, chemical and form instability, lack of uniformity, low water content, odor and active receptivity issues.
Mixing
We believe that we are able to manufacture hydrogel feed mixes with far greater homogeneity than those of our competition. This manufacturing advantage is critical, especially as it relates to dosages of active ingredients. In addition, our proprietary mixing technology allows for the incorporation of sensitive materials that may degrade if subjected to other types of mixing.
Coating
Our proprietary coating technology enables us to properly coat the gels even though the gels are extremely thick and resistant to flow. We have achieved coating tolerances that have allowed us to coat materials as thin as 0.005 of an inch with a margin for error of typically less than 5%. Thickness controls are critical with respect to the performance of many of the end products utilizing our hydrogels, including medical electrodes, transdermal delivery patches and cosmetic patches.
Cross-linking
We cross-link our hydrogels using an electron beam accelerator. Such linking is achieved by introducing a high energy field, created by accelerated electrons, which causes the release of hydrogen atoms and causes carbon molecule covalent bonding. The creation of longer chains of the polymer in the gel increases its molecular integrity, giving the gel characteristics that make it useful in a variety of products.
Contact Us
Manufacturing Facility
Important Notice
Notice: We do not have approval from the U.S. Food and Drug Administration (FDA) or any other governmental agency, whether in the U.S. or abroad, to sell or market any product to treat or cure any disease or condition.